Fluid Path Applications
Fluid path applications involve components that convey fluids. Many of these applications require more exotic resins depending upon the nature of the fluid being conveyed (e.g., blood, bone marrow aspirate, contrast media, reagents, water, etc.). These applications typically involve manifold geometries, critical sealing surfaces with strict flash requirements, and minimal draft that require much more intricate tooling.
In addition, many of these components are required to be molded in clear or translucent material, which magnifies the risk of cosmetic defects in the parts. Advanced takes extra steps in order to minimize cosmetic defects including additional cleaning of the tools, screw/barrel pulls, predictive maintenance of screw/barrel components, and certified operators.
Case Studies
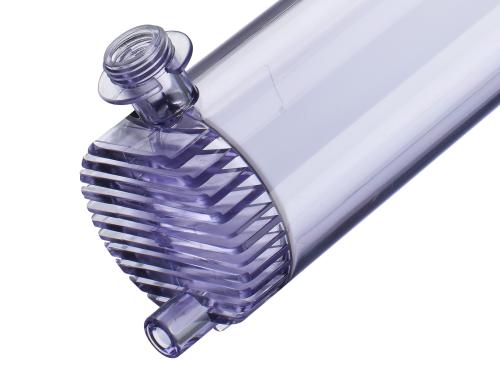
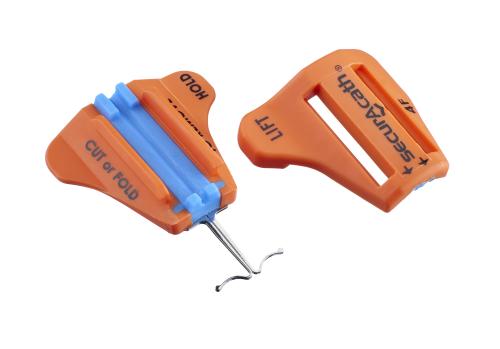
Critical Shutoff Applications
Critical shutoff refers to how tooling components close off against each other during the molding cycle. These shutoffs determine how complex a part can be manufactured and also determine the quality level of the part. Applications include two-shot molding, insert-molding (catheters, gold-plated components, stainless steel tubes, circuit boards, magnets, molded components, etc.), contoured parting lines, interchangeable tooling, spring loaded shutoffs, and telescoping shutoffs. To this day, customers gravitate to Advanced because of the creativity of the tooling approaches to make complex parts. Advanced was founded and owned by a toolmaker after all!
Case Studies
Disciplined Manufacturing
Advanced has a core competency in highly controlled manufacturing methods. Advanced received ISO 13485 in 2010. In 2014, we registered with the FDA. Our first FDA inspection was in 2016 and no 483s were issued. We offer ISO Class 8 (class 100,000) cleanroom molding as well as an Animal Derived Component Free (ADCF) molding cell. We also specialize in validation protocols as required by our customers.
For MedTech and BioTech applications, we conduct installation qualification, operational qualification & performance qualification (IQ/OQ/PQ). In fact, our molding qualification process has been characterized as a best practice by several auditors and medical OEMs.
In addition to molding discipline, Advanced performs final medical device assembly which requires qualified equipment, qualified processes, and stringent documentation (e.g., device history record). This is done in an ISO Class 8 cleanroom (which is designed to and could be qualified to ISO Class 7). Disciplined assembly manufacturing also involves extensive operator training, label making and handling, line clearances, and sterile barrier packaging.
Case Studies
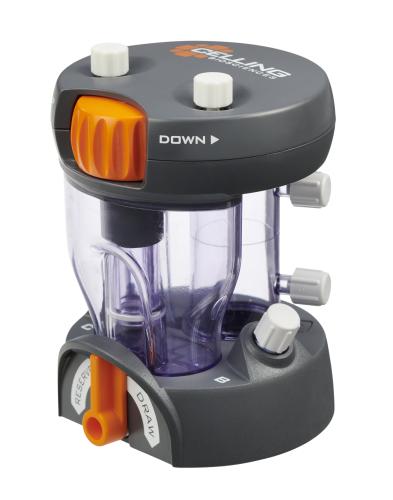
Full Capabilities
Molding
- Class I, II, & III (resins that meet ISO 10993 & USP Class VI)
- Conformal Cooling
- Hardwall & Softwall Cleanroom Molding (Class 7 & 8)
- Insert Molding including robotic handling of inserts (catheters, magnets, molded parts, pins, etc.)
- Integrated 6-Axis Robots
- Roctool Technology
- Small Shot Size Molding (down to 0.2 grams)
- Two-Shot Molding (rotary platen and rotation within the mold)
Secondary Operations
- Adhesive Bonding (UV and Cyanoacrylate)
- Annealing
- Automated Packaging Cell
- Chemical Stress Testing
- Clean Room Assembly (designed to Class 8 & can be qualified to Class 7)
- Corona Treatment
- Dye Penetration and Peel Testing
- EMI/RFI Shielding
- Heat Staking
- Laser Marking
- Leak Testing
- Near Field Communication (NFC) Labeling
- Pad Printing
- Robotic Adhesive Bonding
- Spin Welding
- Sterile Barrier Packaging (tray & pouch)
- UDI Labeling
- Ultrasonic Welding
Qualification & Process Monitoring
- Air Velocity and Particle Concentration Testing (Environment Monitoring)
- Automatic Shot Rejection
- Capability Studies (Cpk, Ppk, including testing for normality, control, etc.)
- CT Scanning
- Design of Experiments (DOE)
- First Article Inspection Report (FAIR)
- Gage Repeatability and Reproducibility (GR&R)
- Instant Measurement Vision System
- IQ/OQ/PQ (Equipment and Process Validation)
- Master Validation Plan (MVP) (process and purchased components)
- Process Failure Modes & Effects Analysis (PFMEA)
- Product Part Approval Process (PPAP)
- Scientific Molding & Scientific Processing
- Statistical Process Control
- Vision Inspection System